Dredging is an essential process in excavation and sediment removal, playing a crucial role in maintaining waterways, restoring shorelines, and enabling construction projects. Whether it’s for mining, environmental restoration, or port maintenance, selecting the right dredge equipment is vital for achieving efficiency and cost-effectiveness. Each dredging project presents unique challenges, requiring careful consideration of equipment specifications to ensure optimal performance.
One of the most critical aspects of selecting dredge equipment is understanding the relationship between pump capacity and cutter power. These two factors directly impact the efficiency of sediment removal, the depth and type of material that can be dredged, and the overall productivity of the operation. An inadequate pump can lead to inefficient material transport, while an underpowered cutter may struggle with compacted or coarse sediments. Ensuring a proper balance between these components helps maximize dredging efficiency and reduce operational costs.
For smaller-scale projects, such as pond dredging equipment, choosing the right combination of pump and cutter power is equally important. Smaller bodies of water often contain fine sediments, organic material, and debris, requiring specialized equipment to prevent blockages and maintain consistent performance. Understanding how pump capacity and cutter power influence dredging results is key to selecting the most effective solution for any project.
Understanding Dredging Equipment and Its Key Components
Overview of Dredging Equipment
Dredging equipment removes sediment, debris, and unwanted materials from bodies of water such as rivers, lakes, harbors, and ponds. This process is critical for maintaining navigability, preventing flooding, and restoring ecosystems. Several types of dredge equipment are available, each designed for specific applications.
Cutter suction dredgers are widely used for large-scale operations where hard or compacted sediments need to be broken up before being transported through a pipeline. Auger dredgers, on the other hand, are well-suited for precision dredging, making them ideal for environmental projects or pond maintenance. Hopper dredgers are designed for deepwater excavation, collecting sediment in onboard storage before relocating it elsewhere.
Pond dredging equipment is commonly used to remove accumulated sediment in residential, industrial, and agricultural ponds for smaller-scale operations. These systems are often compact and designed to operate in shallow waters, ensuring effective sediment removal without disturbing the surrounding ecosystem. Selecting the right dredge equipment depends on factors such as the type of material to be removed, project scale, and environmental considerations.
Key Components of Dredging Equipment
Dredge Pump
The dredge pump is the heart of any dredging system, responsible for transporting sediment and water through pipelines. A high-quality pump ensures efficient material movement with minimal downtime. Pump capacity is crucial in determining the volume of solids that can be moved per hour, directly impacting overall dredging efficiency.
Cutter Head or Auger
The cutter head or auger breaks up sediment before it is pumped away. Cutter heads are typically used in cutter suction dredgers to excavate harder materials, while augers provide more controlled sediment removal. Thus, they are particularly useful in pond dredging equipment and environmental dredging applications.
Power Systems
Hydraulic or electric systems can power dredging equipment. Hydraulic power provides greater force, making it ideal for heavy-duty dredging, while electric-powered systems are often more energy-efficient and environmentally friendly.
Pipeline and Discharge Systems
Pipelines transport dredged materials from the excavation site to the designated discharge area. The efficiency of sediment transport depends on factors like pipeline diameter, pump pressure, and sediment composition. A well-designed pipeline system ensures smooth operations and minimizes blockages, reducing maintenance requirements.
Understanding Pump Capacity in Dredging Operations
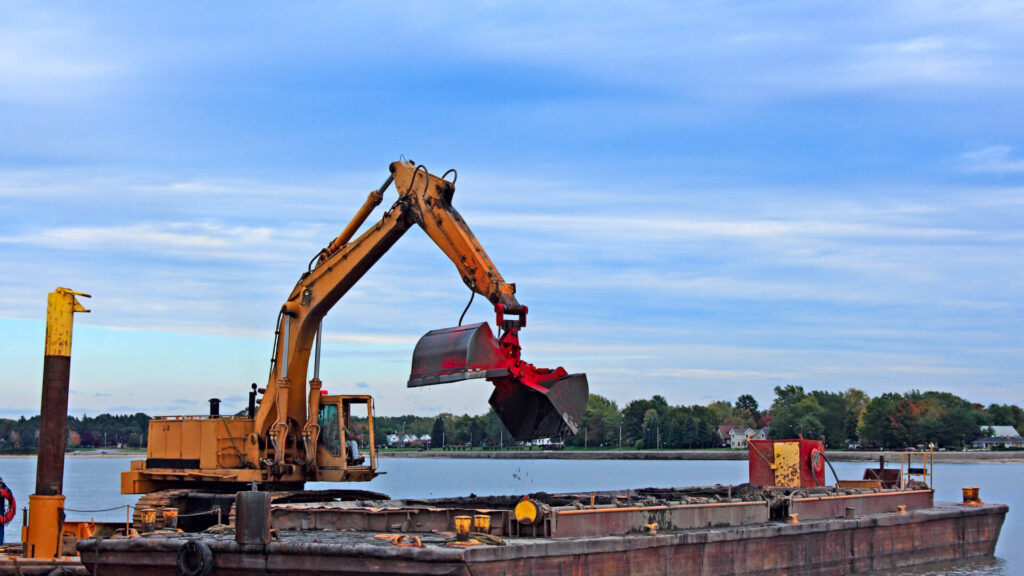
What Is Pump Capacity?
Pump capacity refers to the volume of water and sediment a dredging system can move within a given timeframe. It is one of the most critical factors in dredging operations, directly affecting efficiency, productivity, and overall project success. The right pump capacity ensures that dredge equipment can effectively transport sediment without excessive wear or energy consumption.
Several factors influence pump capacity, including flow rate, head pressure, and efficiency. Flow rate is the amount of material the pump can move per unit of time, typically measured in gallons per minute (GPM) or cubic meters per hour. Head pressure refers to the resistance the pump must overcome to move sediment through pipelines, influenced by pipeline length, diameter, and elevation changes. Efficiency measures how well the pump converts power into effective sediment transport, impacting operational costs and equipment longevity.
How to Determine the Right Pump Capacity
Choosing the appropriate pump capacity requires a detailed assessment of the dredging project. One of the first considerations is the type of sediment being removed. Fine sand and silt require different pump capabilities than heavy clay or coarse gravel. Understanding the material composition ensures that the pump can handle the project’s specific demands without clogging or excessive wear.
Another key factor is matching pump specifications to project needs. Dredge equipment used for large-scale operations, such as mining or harbor maintenance, requires high-capacity pumps to manage significant sediment loads efficiently. On the other hand, pond dredging equipment is designed for smaller-scale projects, where a lower-capacity pump may be sufficient to remove accumulated organic material and fine sediments without overburdening the system.
Common mistakes in selecting pump capacity include underestimating sediment type, choosing an oversized pump that wastes energy, or using a pump with insufficient head pressure. These errors can lead to inefficiencies, increased costs, and premature equipment failure.
Impact of Pump Capacity on Performance
An underpowered pump can result in slow dredging operations, frequent clogs, and excessive downtime. Conversely, an oversized pump may consume unnecessary fuel and increase wear on dredge equipment components. Balancing pump capacity with project needs optimizes efficiency, reduces fuel consumption, and extends equipment lifespan.
For example, pond dredging equipment with the right pump capacity can operate continuously without overwhelming the system, ensuring effective sediment removal with minimal maintenance. Real-world case studies demonstrate that selecting the correct pump can improve dredging speed, lower operational costs, and enhance overall project efficiency.
Cutter Power and Its Role in Dredging Efficiency
What Is Cutter Power?
Cutter power refers to the force applied by the cutter head or auger to break up and loosen sediment before it is transported through the dredging system. It plays a crucial role in determining how effectively dredge equipment can remove different types of materials, from soft mud to compacted clay and rocky formations. The right cutter power enhances dredging speed, reduces operational strain, and ensures that sediment is properly fragmented for efficient pumping.
A well-matched cutter head and pump system allow for continuous operation without clogging or excessive wear. Insufficient cutter power can slow down the dredging process, forcing the pump to work harder and reducing overall efficiency. Excessive cutter power can also lead to unnecessary fuel consumption and increased wear on dredging components. Balancing cutter power with pump capacity is key to optimizing performance.
Selecting the Right Cutter Power for Your Project
Choosing the appropriate cutter power depends on the type of sediment being dredged. Soft materials like silt and mud require less power, while compacted sediments, clay, and hard-packed sand demand a more robust cutter to break them apart efficiently. If the cutter is too weak, dredge equipment may struggle to maintain a consistent material flow, leading to delays and inefficiencies.
Cutter power also directly affects wear and tear on dredging equipment. Excessive force on soft materials can cause unnecessary blade wear, while insufficient power in tougher conditions can overwork the system, leading to premature mechanical failures. Properly selecting cutter power helps extend the life of key components, reducing maintenance costs and downtime.
In smaller-scale operations, such as those using pond dredging equipment, cutter power must be carefully calibrated to avoid disturbing the surrounding environment. Since pond dredging equipment is typically used in sensitive areas, selecting a cutter that efficiently breaks up sediment without excessive force ensures that the operation remains effective while minimizing environmental impact.
Achieving the right balance between cutter power and pump efficiency is essential for maximizing dredging productivity. When these components work in harmony, the dredging process becomes more efficient, cost-effective, and sustainable.
Matching Pump Capacity with Cutter Power for Optimal Performance
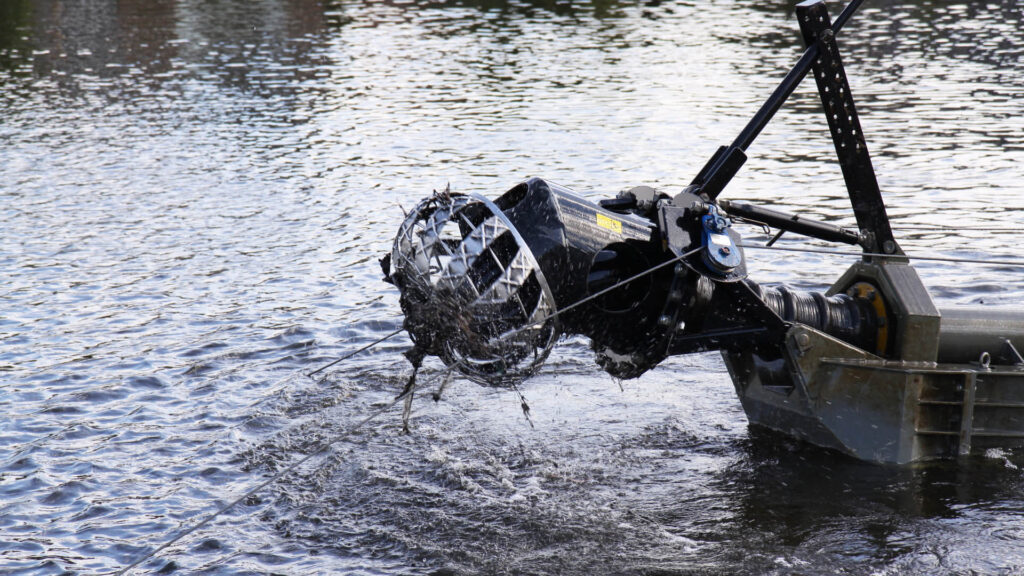
Why a Balanced System Matters
Achieving the right balance between pump capacity and cutter power is crucial for efficient dredging operations. If these components are not properly matched, dredge equipment may experience bottlenecks that reduce efficiency, increase fuel consumption, and strain mechanical components. The cutter must be powerful enough to break down the sediment effectively, but if it generates more material than the pump can handle, clogging and reduced suction efficiency may occur. Conversely, if the pump is too powerful for the cutter, it may not receive a steady flow of loosened sediment, leading to wasted energy and reduced operational output.
Misalignment between these two critical components can significantly impact overall dredging efficiency. When the system is unbalanced, dredge equipment requires more power to compensate, increasing fuel costs and accelerating wear on key components. This is especially critical in applications such as pond dredging equipment, where operations often take place in smaller, more controlled environments. In these cases, excessive cutter power or an overpowered pump can lead to unnecessary disruption of the surrounding area, making precision even more important.
Optimizing Pump and Cutter Performance Together
To maximize efficiency, operators must carefully calibrate pump capacity with cutter power. One best practice is assessing sediment composition and ensuring that the cutter is designed to handle the material effectively before the pump transports it. Soft sediments like mud and silt require moderate cutter power, while harder materials such as clay or compacted sand demand a more powerful cutter to prevent excessive strain on the pump.
Modern dredging equipment benefits from advanced automation and control systems that help optimize pump and cutter performance. These systems continuously monitor flow rates, cutter resistance, and sediment density to make real-time adjustments. This level of precision ensures that dredge equipment operates at peak efficiency, reducing fuel consumption and extending the lifespan of critical components.
In real-world applications, well-calibrated pond dredging equipment has proven to improve project efficiency significantly. By balancing cutter power and pump capacity, operators can avoid unnecessary downtime, ensure smooth sediment removal, and reduce overall maintenance costs, ultimately achieving more productive and cost-effective dredging operations.
Choosing the Best Dredging Equipment for Your Project
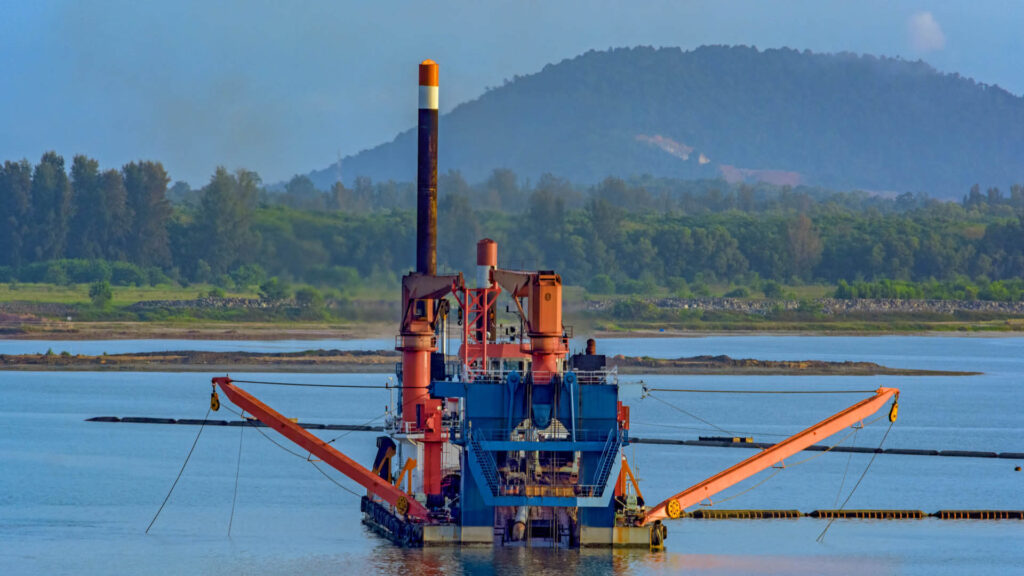
Factors to Consider in Equipment Selection
Selecting the right dredging equipment for a project requires careful evaluation of several factors to ensure optimal efficiency and cost-effectiveness. One of the most important considerations is the size and scope of the project. Large-scale dredging operations, such as port maintenance or mining, require powerful dredge equipment with high-capacity pumps and heavy-duty cutter heads. In contrast, smaller-scale projects, such as pond dredging equipment applications, demand compact, maneuverable dredgers that can operate efficiently in shallow waters without disturbing the surrounding environment.
Environmental factors also play a crucial role in equipment selection. The type of sediment being dredged—whether it’s fine silt, compacted clay, or rocky debris—determines the necessary cutter power and pump capacity. Additionally, projects in ecologically sensitive areas require dredging equipment that minimizes turbidity and protects aquatic life.
Budget constraints and operational cost efficiency should also be considered. While high-performance dredgers may have a higher upfront cost, they often offer greater efficiency, reducing fuel consumption and maintenance expenses over time. Selecting equipment that aligns with project needs while optimizing long-term costs ensures a successful operation.
Customization and Modifications for Specific Needs
Dredging projects vary widely, and sometimes standard equipment configurations may not be sufficient. Specialized cutter heads can significantly improve efficiency when dealing with unique dredging challenges, such as removing compacted sediments or operating in environments with high debris levels. These modifications ensure that dredge equipment is tailored to the specific conditions of a project, improving overall performance.
Upgrading pump components can also enhance durability and longevity. Higher-quality materials for pump casings and impellers reduce wear and extend operational life, minimizing downtime and maintenance costs. Whether it’s a large-scale operation or a small pond dredging equipment project, investing in the right upgrades ensures that the dredging process remains efficient and cost-effective.
Conclusion
Selecting the right pump capacity and cutter power is essential for ensuring efficient and cost-effective dredging operations. These two factors directly influence the performance of dredging equipment, affecting material removal rates, fuel consumption, and overall project success. A well-balanced system prevents bottlenecks, reduces component wear, and maximizes productivity. Whether working on large-scale dredging projects or using pond dredging equipment for smaller applications, aligning pump and cutter specifications with the project’s specific needs is crucial.
Operators should carefully evaluate sediment type, equipment capabilities, and environmental conditions to maximize efficiency and minimize operational costs. Investing in properly calibrated dredging equipment, leveraging automation systems, and selecting high-quality components can significantly improve dredging outcomes.
For those unsure of the best equipment configuration for their needs, consulting with dredging experts is highly recommended. Industry professionals can provide tailored recommendations to ensure optimal performance, extend equipment lifespan, and reduce downtime. By making informed decisions, operators can achieve sustainable and efficient dredging operations across various applications.