Effective water management stands at the core of profitable and safe mining. Whether a site is carved into a mountainside or extends deep beneath it, uncontrolled groundwater and storm runoff can halt production, destabilize workings, and inflate maintenance budgets. Modern mining submersible pumps have emerged as the workhorse of dewatering strategies, operating directly in flooded zones to move high volumes of sediment-laden water without constant operator intervention. Their compact design, rugged materials, and automated controls make them indispensable in both open-pit pits and the confined headings of underground mines, where space, access, and uptime are at a premium.
By positioning the pump at the water source rather than above it, operators eliminate priming issues, reduce suction losses, and cut energy consumption. The result is a safer pit wall, drier haul roads, and stable underground headings, all of which translate into fewer stoppages and measurable cost savings. In short, mining submersible pumps are not just a dewatering tool; they are an operational safeguard that underpins productivity across the entire life of a mine.
The Role of Dewatering in Mining Operations
Water Challenges in Open-Pit vs. Underground Mines
Open-pit operations must contend with direct rainfall, stormwater sheet flow, and seepage through fractured geology. Left unchecked, ponding water softens haul-road surfaces, increases rolling resistance, and accelerates tire wear on heavy equipment. Underground mines face a distinct threat profile, including aquifers intersected during development, pressurized fissures, and seasonal inflows that can flood declines and shafts. In both settings, stagnant water corrodes structural steel, short-circuits electrical infrastructure, and compromises slope or roof stability, risks that escalate maintenance costs and expose crews to hazards.
Why Dewatering Is a Critical Operational Priority
Every unplanned stop to pump out flooded headings translates directly into lost ore tonnage and revenue. Proactive dewatering ensures that drills, loaders, and conveyors operate on schedule, keeping the mine’s production curve on target. Moreover, regulators are increasingly mandating active water-management plans that prevent the discharge of contaminated runoff into local waterways. Deploying submersible pumps for mining sector compliance not only protects the environment but also shields operators from fines and reputational damage.
Finally, efficient water control underpins asset longevity. Dry mechanical chambers, electrical rooms, and haul routes reduce corrosion, extend component life, and decrease the frequency of overhauls. Here, rugged submersible mining pumps deliver consistent flow rates and abrasive-handling capability that alternative surface units cannot match, sustaining both safety metrics and bottom-line performance.
What Are Mining Submersible Pumps and Why Are They Ideal?
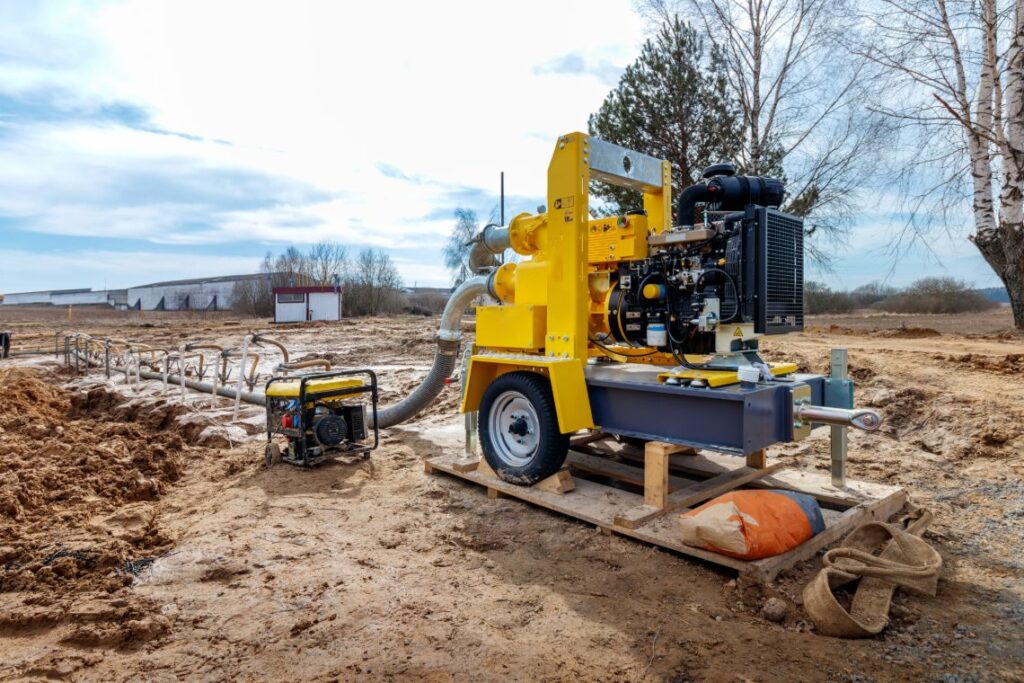
Modern mining submersible pumps are purpose-built centrifugal units whose motors and hydraulics are sealed within a water-tight housing, allowing the entire assembly to run fully submerged at the fluid source. By removing the suction lift altogether, these pumps maintain a constant prime, reduce NPSH concerns, and deliver stable flow under fluctuating heads, capabilities that conventional skid or trailer units struggle to match in dynamic mine conditions.
Key Design Features of Submersible Mining Pumps
- Fully submerged operation – Operating at the bottom of a sump or well, mining submersible pumps avoid cavitation, eliminate suction piping, and keep noise levels below ground.
- Abrasion- and corrosion-resistant materials – Chromium-alloy impellers, urethane coatings, and 316 SS fasteners give submersible pumps for mining sector applications the durability needed to handle acidic groundwater and sharp silica fines.
- High solids handling capacity – Impeller vanes and volutes are engineered with wide passages, allowing submersible mining pumps to pass particles up to 75 mm, thereby preventing blockages that sideline traditional clear-water pumps.
Advantages Over Other Pump Types
- Compact footprint in confined spaces – At barely half the footprint of a skid pump plus suction hose, a single mining submersible pump can fit inside narrow development drifts or beneath haul-road causeways without disrupting traffic.
- Minimal priming or setup – Simply drop the unit, connect power, set the discharge hose, and start pumping; no foot valves or vacuum assists are required, significantly reducing setup time for crews already managing tight production schedules.
- High reliability in challenging site conditions – With no belts, couplings, or exposed shafts, mining submersible pumps keep critical components underwater and away from abrasive airborne dust, translating into fewer unscheduled pull-outs for repairs.
Dewatering in Underground Mining: Systems and Submersible Pump Applications
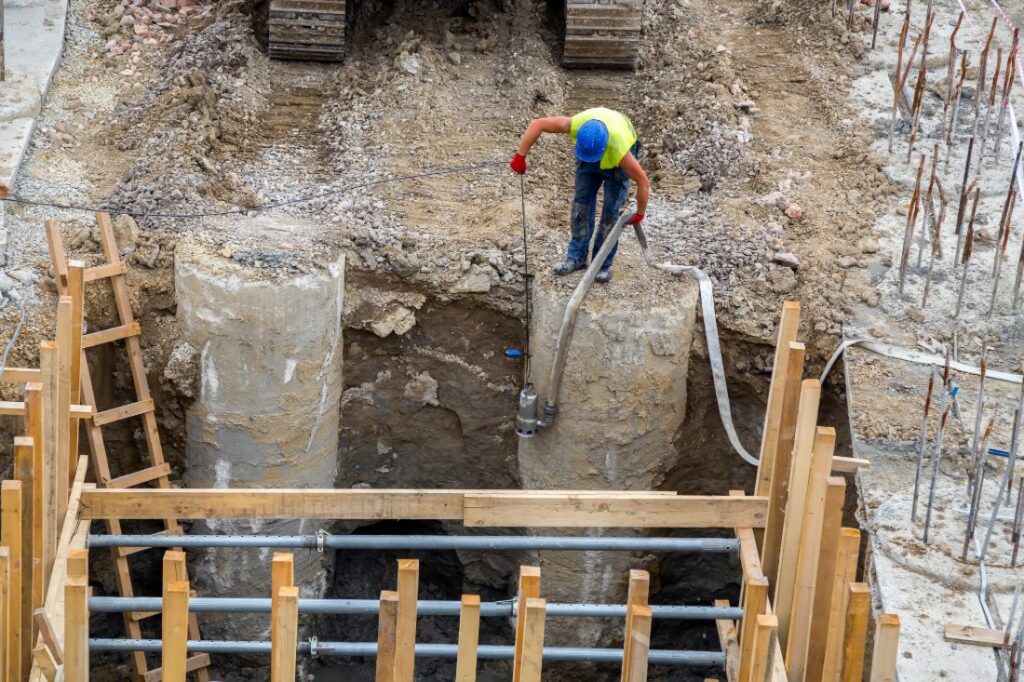
Components of an Underground Dewatering System
Engineering teams typically combine drilled vertical wells that lower piezometric pressure, horizontal drains that intercept face inflows, rock-bolted collection gutters, and strategically located sumps to manage groundwater. These sumps channel water toward either single-stage submersible pumps for mining sector duties or multistage booster strings that lift water hundreds of metres to the surface. Vacuum lines and sensors integrate into the mine’s SCADA system, allowing operators to view inflow trends in real-time.
How Submersible Pumps Fit In
Placed at each low point, mining submersible pumps automatically start when float switches detect rising water. The pumps’ recessed-vortex or semi-open impellers clear grit, cutting chips, and shotcrete spatter without clogging, a critical advantage as crews blast and muck out headings. Because thermal sensors and moisture probes are embedded in the stator, the mine control room can receive an alarm long before a bearing overheats or a seal fails, allowing technicians to service the unit during planned downtime. For deeper shafts, chains of submersible mining pumps staged at intermediate levels overcome static head while simplifying hose routing and power supply.
Safety and Efficiency Benefits
By extracting water at its point of accumulation, submersible pumps for mining sector operations keep footwall travelways dry, reducing slip incidents and allowing diesel and electric LHDs to maintain design speeds. Clear working faces enable accurate drill-and-blast patterns, while dry explosives remain stable and predictable. Importantly, workers spend less time in flooded areas setting temporary pipework; a single hook, power cable, and lay-flat discharge are all a crew needs to reposition submersible mining pumps as the mine advances. Continuous, automatic dewatering maximises face time, minimises electrical downtime, and preserves ground support integrity across every shift.
Open-Pit Dewatering: The Open Sump Pumping Method
In an open-pit mine, rainfall, groundwater seepage, and wash‐down water all gravitate to the lowest benches. Operators excavate purpose-built sumps at these points and install mining submersible pumps directly inside the collection pit. Because the pump and motor are submerged, flow begins immediately and continues even as water levels fluctuate, keeping haul roads passable and pit walls stable.
How It Works – As water drains into the sump, sensors or float switches trigger the pump to lift the inflow through a lay-flat hose to a settling pond or discharge header well outside the excavation zone. The self-priming nature of mining submersible pumps eliminates the need for vacuum assist systems, allowing crews to deploy extra units within minutes when a monsoon front or sudden storm threatens production. For contractors seeking rapid deployment, submersible pumps for mining sector applications offer a plug-and-play solution that integrates seamlessly with existing power distribution skids.
Where Submersible Pumps Excel – Unlike skid-mounted units that crowd bench space, the slim profile of mining submersible pumps allows them to sit flush with the pit floor, leaving runways clear for trucks and loaders. As the excavation deepens or shifts laterally, a crane simply lifts the unit, repositions the discharge line, and drops it back into the newly cut sump, preserving optimal head pressure. When emergency over-topping occurs, a crew can lower additional submersible mining pumps to reinforce capacity without halting ore loading.
Limitations and Workarounds – Extremely deep water tables may exceed a single pump’s head rating. Staged pumping, using submersible pumps for mining sector duty at floor level, and feeding a booster set halfway up the ramp, solves the problem while minimizing hose friction losses. Soil erosion around the sump can be controlled with geotextile liners and rock armoring. At the same time, sacrificial screens prevent oversized rocks from striking the impeller, ensuring each mining submersible pump meets its design life between scheduled rebuilds.
Choosing the Right Pump: Comparing Mining Pump Technologies
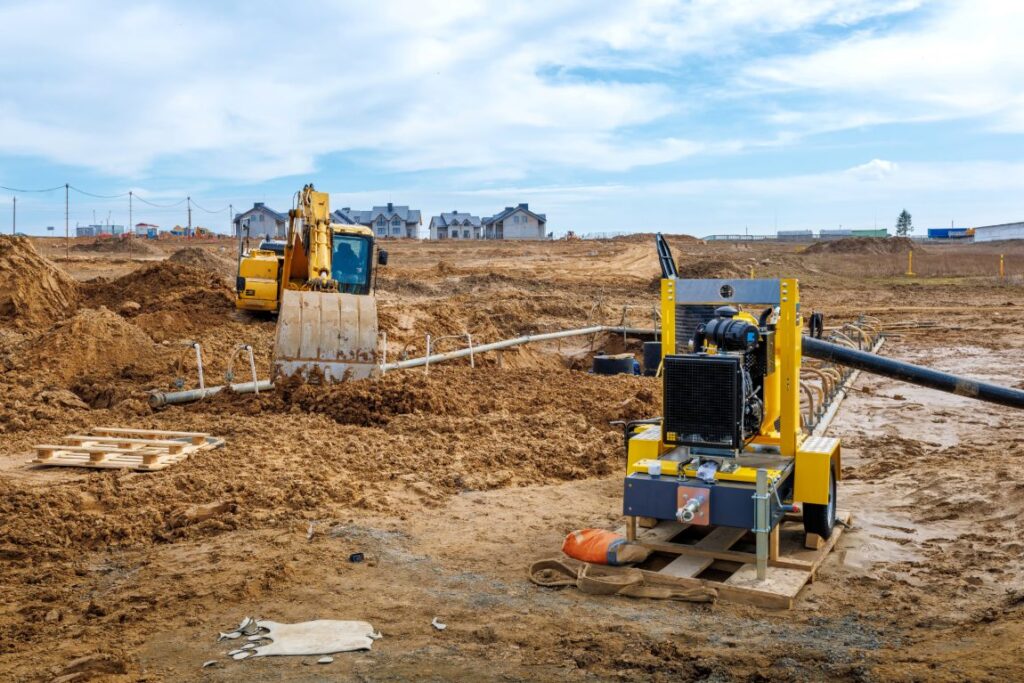
Selecting the appropriate pump technology is essential to maintaining uptime and cost efficiency in mining operations. The choice depends on the site’s depth, water volume, slurry content, and chemical composition. While multiple options exist, mining submersible pumps are often the preferred solution due to their adaptability, durability, and low maintenance profile.
Overview of Common Mining Pump Types and Their Applications:
- Submersible Pumps
Ideal for deep pits, sumps, and confined spaces.
➤ Operate while fully submerged
➤ Excellent solids-handling capacity
➤ Highly durable in harsh environments - Centrifugal Pumps
Best suited for moving large volumes of water over short distances.
➤ High flow rates
➤ Simple maintenance
➤ Commonly used in surface-level applications - Slurry Pumps
Specifically designed for transporting abrasive slurries, tailings, and ore.
➤ Heavy-duty construction
➤ High wear resistance
➤ Optimized for consistent slurry handling - Positive Displacement Pumps
Used when fluid viscosity is high and precise flow is required.
➤ Delivers a constant flow regardless of discharge pressure
➤ Ideal for metering applications or thick fluids - Piston/Diaphragm Pumps
Effective for handling fluids with extremely high solids content.
➤ Minimal risk of clogging
➤ Excellent for sludge or paste backfill - Surface Pumps
Positioned outside the sump for easy access and serviceability.
➤ Best for shallow water removal
➤ Easy to install and relocate - High-Wall Pumps
Installed on bench walls or slopes in open-pit mines.
➤ Mobile and modular
➤ Targets specific dewatering zones with minimal infrastructure
Why Submersible Units Often Deliver the Best ROI – First, a sealed motor means no alignment checks, belt swaps, or open shafts exposed to dust, resulting in fewer person-hours spent on maintenance and more tonnes moved per shift. Second, with only a power cable and discharge hose topside, mining submersible pumps limit the parts inventory that procurement teams must stock, lowering capital tied up in spares. Third, their abrasion-resistant casings and elastomer liners extend the mean time between overhauls, allowing a fleet of submersible mining pumps to remain in-pit throughout entire rainy seasons without withdrawal. For mixed-ore sites where fines, clay, and shot rock arrive in waves, submersible pumps for mining sector programs provide the flow stability planners need to keep crushers fed and mills running smoothly.
By combining lower downtime, reduced spares, and simplified logistics, mining submersible pumps consistently outperform surface-mounted alternatives in terms of total cost of ownership. Their long sealing life and built-in thermal and moisture protection further shield production schedules, key benefits that explain why many purchasing managers now standardize on fleets of rugged submersible mining pumps across global assets.
Real-World Applications and Deployment Best Practices
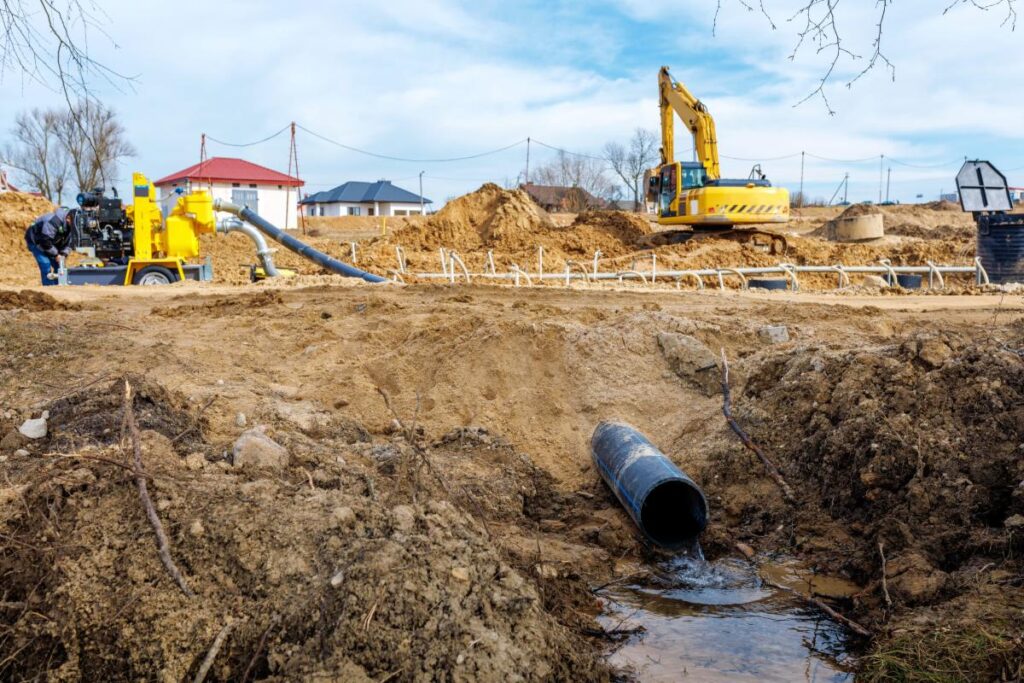
Across challenging field conditions, mining submersible pumps have proven indispensable. During an emergency flood response at a Southeast Asian open-pit mine, a fleet of mining submersible pumps was lowered into freshly cut sumps within two hours of an approaching typhoon. Their submerged operation allowed continuous dewatering while haulage quickly resumed, averting slope failure and equipment loss.
In a Philippine copper operation, engineers installed a cascading, multi-level system using mining submersible pumps along the decline. The staged lift reduced hose friction, and each unit’s moisture probes relayed data to the control room, enabling predictive maintenance. Because these submersible pumps for mining sector duties handled 65 mm debris, blockages from shot-rock fragments were virtually eliminated.
Municipal agencies have adopted the same technology for rapid flood mitigation. When torrential rains overwhelmed drainage canals, crews deployed containerised skids carrying mining submersible pumps that discharged directly into storm sewers. The compact footprint met strict urban right-of-way limits, exemplifying how submersible mining pumps deliver industrial performance in emergency civil works.
Key Factors for Effective Deployment
- Accurate sizing – Match flow, head, and solids loading before selecting mining submersible pumps; oversizing wastes energy, undersizing accelerates seal wear.
- Material selection – Specify high-chrome iron, duplex stainless, or elastomer-lined volutes where sand, quartz, or acidic water prevail to extend submersible mining pumps’ service life.
- System integration – Pair submersible pumps for mining sector applications with level transmitters, VFDs, and SCADA systems to automate start/stop cycles, amperage trends, and maintenance alerts.
Final Considerations: Procurement and System Design Insights
Technical Evaluation Checklist
- Duty-point confirmation – Ensure the proposed mining submersible pumps deliver the required flow at the design head with at least a 20% reserve for surge events.
- Motor protection – Specify thermal overloads, phase monitors, and VFD-compatible windings to ensure submersible pumps for mining sector projects can handle fluctuating inflows without stalling.
- Support and service – Choose suppliers that stock seals, cables, and wear rings locally; fast turnaround keeps submersible mining pumps in circuit and avoids wet-hire costs.
Long-Term Value Metrics
- Reduced replacements – Corrosion-resistant casings enable mining submersible pumps to outlast surface units by several seasons, cutting capital spend.
- Higher uptime – Remote telemetry warns of seal leakage or overload, allowing crews to swap units before sumps overflow, thereby sustaining production.
- Scalable systems – As pits deepen, additional submersible pumps for mining sector expansion can be craned in and wired to existing panels, eliminating the need for redesign costs.
These submersible mining pumps continue to set new benchmarks for efficiency in both brownfield and greenfield operations.
Why Submersible Pumps Are Essential for Safe and Efficient Mining
Effective dewatering is never a one-size-fits-all exercise; every ore body, hydrogeological profile, and production schedule demands a solution engineered to fit. Well-designed systems built around mining submersible pumps maintain solid haul roads, keep underground headings dry, and ensure regulatory compliance, thereby protecting both personnel and profits.
By operating at the water source, submersible pumps for the mining sector’s requirements combine superior solids handling with low maintenance overhead, delivering the safety, efficiency, and long-term durability that planners and procurement teams expect. In surface pits or deep declines alike, rugged submersible mining pumps prevent costly downtime and extend equipment life, ultimately safeguarding return on capital.For a system that matches your exact flow, head, and abrasion conditions, consult with specialist engineers who understand the nuances of pump curves, motor protection, and SCADA integration. Contact Dredge Pump Pros today for expert guidance and reliable access to high-performance mining submersible pumps specifically designed for your site conditions.