Mining pumping systems play a crucial role in mining operations, where the efficient movement of water, slurry, and chemicals is vital to the extraction and processing of minerals. Whether it’s dewatering a mine, transporting abrasive slurries, or implementing chemical pumping solutions, these pumps are indispensable for maintaining smooth operations. In modern mining, the focus is not only on reliability but also on achieving optimal safety and industrial pump efficiency.
The high-stakes nature of mining means that equipment failure or downtime can result in significant financial losses and even pose safety risks. By prioritizing efficient and safe mining pumping systems, mining companies can boost productivity while ensuring worker safety and environmental protection. This article explores the types of mining pumping systems used in the industry and the measures that enhance both industrial pump efficiency and safety.
2. Types of Pumping Systems Used in Mining
There are various mining pumping systems used in mining, each suited to specific tasks and operating conditions. The four most common types are centrifugal pumps, positive displacement pumps, submersible pumps, and chemical handling pumps, all of which contribute to optimizing industrial pump efficiency in different mining applications.
Centrifugal Pumps
Centrifugal pumps are among the most widely used in mining, especially for dewatering operations and slurry transport. These pumps work by converting rotational kinetic energy into hydrodynamic energy to move liquids, making them effective at handling large volumes of fluid. In mining, centrifugal pumps are typically employed to move water or low-viscosity slurries.
One key benefit of centrifugal pumps is their simplicity of design and ease of maintenance. They are cost-effective for moving high volumes of material over long distances. However, these pumps can face challenges when dealing with highly abrasive or thick slurries, which can cause internal wear and reduce efficiency. In situations where hazardous chemicals are involved, chemical pumping solutions may be required to ensure safe and efficient transport. Routine maintenance is essential to mitigate these issues and maintain optimal performance.
Positive Displacement Pumps
When dealing with high-viscosity fluids or abrasive materials, positive displacement pumps are often the preferred choice in mining operations. Unlike centrifugal pumps, which rely on kinetic energy, positive displacement pumps trap a fixed amount of fluid and push it through the system. This makes them ideal for handling slurries, thick liquids, and abrasive materials.
Positive displacement pumps come in various types, including diaphragm pumps, piston pumps, and peristaltic pumps. Diaphragm pumps are particularly effective at handling slurries, while peristaltic pumps excel in managing fluids containing abrasive solids. The ability of positive displacement pumps to handle challenging materials with minimal wear makes them valuable in mining environments where durability is essential.
Submersible Pumps
Submersible pumps are critical in underground mining pumping systems, where dewatering is a constant necessity. These pumps are designed to operate while fully submerged in the fluid they pump, allowing for the efficient removal of water from flooded areas, pits, and groundwater sources. Positioned directly in the fluid, submersible pumps are protected from external damage, making them durable and ideal for harsh mining environments.
Submersible pumps also offer the advantage of operating quietly and efficiently. They play a vital role in keeping mining operations safe by preventing water accumulation that could disrupt activities or cause safety hazards, making them an essential part of reliable mining pumping systems.
Chemical Handling Pumps
Mining operations often require the transport of hazardous chemicals, necessitating specialized chemical handling pumps. These pumps are designed to meet stringent safety and durability standards to ensure that toxic or corrosive chemicals are moved without leaks or spills. Chemical handling pumps are equipped with features like double seals and corrosion-resistant materials to safeguard both workers and the environment.
By using pumps specifically designed for chemical pumping solutions, mining companies can reduce the risk of contamination and accidents, ensuring safe and compliant transport of hazardous materials. These chemical pumping solutions play a crucial role in maintaining operational safety and environmental compliance in the mining industry.
3. Enhancing Efficiency in Mining Pumping Systems
Efficiency is a key focus in mining, where reducing operational costs and energy consumption is critical to maintaining profitability. Modern technologies are enhancing industrial pump efficiency in mining pumping systems in several ways, helping to streamline operations and lower overall energy use.
Energy Optimization with Variable Frequency Drives (VFDs)
One of the most effective methods for improving industrial pump efficiency in mining pumping systems is the integration of Variable Frequency Drives (VFDs). VFDs allow pumps to adjust motor speed based on the required flow rate, optimizing energy consumption in real-time. This reduces unnecessary energy use when demand is low, ultimately lowering operational costs and enhancing overall efficiency.
In mining, where fluid volumes can fluctuate, VFDs provide a flexible and energy-efficient solution. By matching pump output to actual requirements, VFDs not only save energy but also extend the lifespan of the pumps by preventing excessive wear and tear.
Automated Monitoring Systems
Automated monitoring systems offer real-time tracking of pump performance, allowing operators to detect issues before they escalate into costly failures. These systems monitor key metrics such as flow rate, pressure, and energy consumption, providing valuable insights into the efficiency of pumping operations.
By using automated systems, mining companies can optimize pump performance, schedule maintenance proactively, and prevent downtime. This not only results in smoother operations but also significantly enhances industrial pump efficiency, leading to a reduction in operational delays and improved overall productivity.
Minimizing Downtime
Minimizing downtime is essential in mining, where interruptions can be costly. Routine maintenance is critical for ensuring that mining pumping systems continue to operate efficiently, directly contributing to industrial pump efficiency. Automated technologies, such as smart sensors and monitoring systems, help identify potential problems early, allowing operators to address issues before they lead to breakdowns.
This proactive approach to maintenance keeps mining pumping systems running smoothly and reduces the risk of unplanned outages that could slow down production, ultimately improving industrial pump efficiency and ensuring consistent, reliable operations.
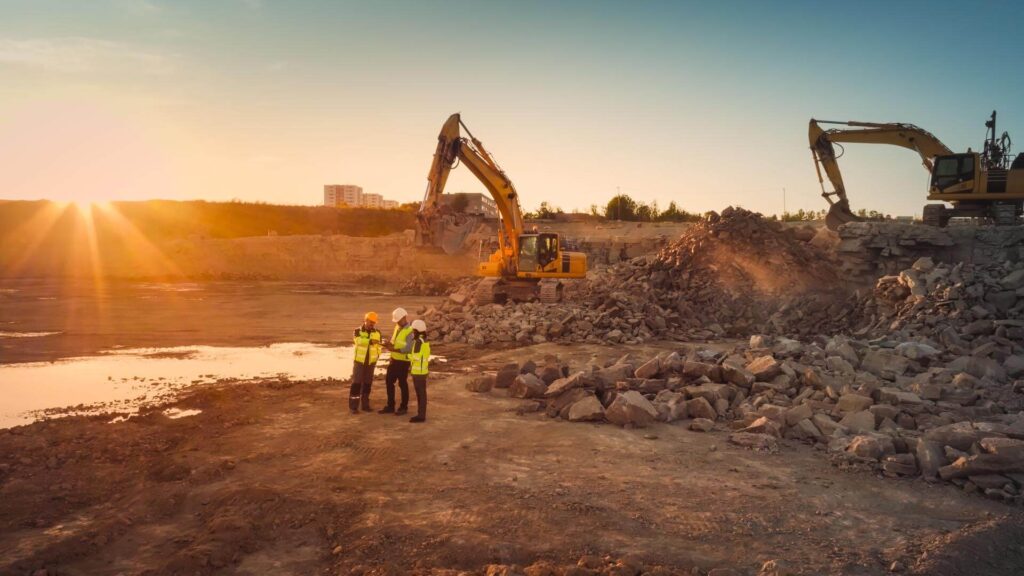
4. Ensuring Safety in Mining Pumping Systems
Safety is paramount in mining operations, and mining pumping systems play a vital role in maintaining a safe working environment. Several features are essential to ensure the safety of pumping systems in mining.
Overpressure Protection Devices
Pumping systems in mining must be equipped with overpressure protection devices, such as pressure relief valves, to prevent equipment failure. These devices monitor the system’s pressure levels and automatically release pressure when it reaches unsafe levels, reducing the risk of accidents and protecting equipment from damage.
Corrosion-Resistant and Abrasion-Resistant Materials
Mining is a harsh environment where pumps are exposed to abrasive materials and corrosive chemicals. Using pumps made from corrosion-resistant and abrasion-resistant materials ensures durability and extends the life of the equipment. This not only enhances safety but also reduces the frequency of maintenance and replacement, contributing to overall industrial pump efficiency.
Handling Hazardous Materials
In addition to the physical wear on pumps, handling hazardous materials requires specialized safety features. Pumps designed for chemical handling are equipped with double-seal mechanisms and built from materials that can withstand corrosive substances. These safety measures are crucial for preventing leaks, spills, and environmental contamination, thereby ensuring worker safety.
5. Best Practices for Maintaining Mining Pumping Systems
Regular maintenance and operator training are essential to maximize the efficiency and safety of mining pumping systems.
Scheduled Maintenance and Inspections
Routine inspections and scheduled maintenance are necessary to keep pumps in optimal condition. Regular checks allow for early detection of wear or damage, preventing small issues from becoming major problems. By adhering to a maintenance schedule, mining operators can ensure that their pumps function efficiently and avoid costly downtime.
Training and Safety Protocols
Proper training ensures that workers are equipped to operate and maintain mining pumping systems safely. Operators should be familiar with the specific safety features of the pumps they handle and trained in responding to emergencies. Comprehensive safety protocols should be in place to guide workers in maintaining pumps and addressing any issues that arise.
6. Conclusion
Mining pumping systems are essential for the safety and efficiency of modern mining operations. By utilizing the right types of pumps—whether centrifugal, positive displacement, submersible, or chemical handling pumps—mining companies can enhance both productivity and safety. The integration of modern technologies, such as Variable Frequency Drives and automated monitoring systems, further boosts industrial pump efficiency, while regular maintenance and safety features protect both workers and equipment. Additionally, chemical pumping solutions ensure the safe transport and handling of hazardous materials, further contributing to the overall safety and compliance of mining operations.
As mining operations continue to evolve, advancements in pumping technology will play an increasingly important role in ensuring safer, more efficient mining operations. By focusing on both safety and efficiency, mining companies can optimize their pumping systems and meet the demands of the industry while maintaining a secure working environment.